Die casting in Malaysia has become an essential component of the manufacturing industry, playing a critical role in producing high-quality metal parts for various applications. As the country continues to develop its industrial capabilities, die casting has emerged as a key process in sectors such as automotive, aerospace, electronics, and consumer goods. The ability to create precise and durable components using die casting has attracted both local and international businesses to invest in Malaysia’s manufacturing sector. With a strong infrastructure, skilled workforce, and government support for industrial growth, Malaysia has positioned itself as a competitive hub for die casting production. Companies involved in this industry leverage advanced technology and automation to enhance efficiency and meet global quality standards. As demand for lightweight, high-performance metal parts continues to rise, Malaysia’s die casting sector is expected to experience further expansion.
One of the major advantages of die casting is its ability to produce complex shapes with high accuracy and consistency. The process involves injecting molten metal into a mold cavity under high pressure, allowing manufacturers to create intricate designs with minimal machining. This makes die casting a cost-effective solution for mass production, as it reduces material waste and increases production speed. Malaysia’s die casting companies have adopted state-of-the-art machinery and innovative techniques to improve product quality and efficiency. The industry has seen significant advancements in automation, enabling manufacturers to streamline operations and maintain consistency across large-scale production. With the integration of computer-aided design (CAD) and simulation software, companies can optimize mold designs and enhance production outcomes. These technological advancements have positioned Malaysia as a leader in die casting, capable of meeting the evolving demands of global industries.
The automotive industry is one of the biggest beneficiaries of die casting in Malaysia, relying on this process to manufacture essential vehicle components. Lightweight aluminum and zinc die-cast parts are widely used in modern automobiles to enhance fuel efficiency and reduce overall weight. Components such as engine blocks, transmission cases, and structural brackets are commonly produced using die casting due to their strength and durability. Malaysia’s strategic location and well-established supply chains have attracted major automotive manufacturers to set up production facilities in the country. The demand for high-precision automotive parts continues to grow, prompting local die casting companies to invest in research and development. By focusing on material innovation and process improvements, Malaysian manufacturers are able to produce high-quality components that meet international automotive standards. This has strengthened Malaysia’s position as a reliable supplier in the global automotive market.
In addition to the automotive sector, the electronics industry in Malaysia heavily relies on die casting for the production of various components. With Malaysia being a leading exporter of electronic goods, die-cast parts are essential in the manufacturing of housings, heat sinks, and connectors. The precision and thermal conductivity of die-cast aluminum make it an ideal material for electronic applications, ensuring the efficient performance of devices. The growing demand for consumer electronics, telecommunications equipment, and industrial machinery has further fueled the need for high-quality die casting solutions. Malaysian manufacturers have responded by adopting stringent quality control measures and investing in automation to meet the increasing production demands. The ability to produce lightweight and durable electronic components has positioned Malaysia as a key player in the global electronics supply chain.
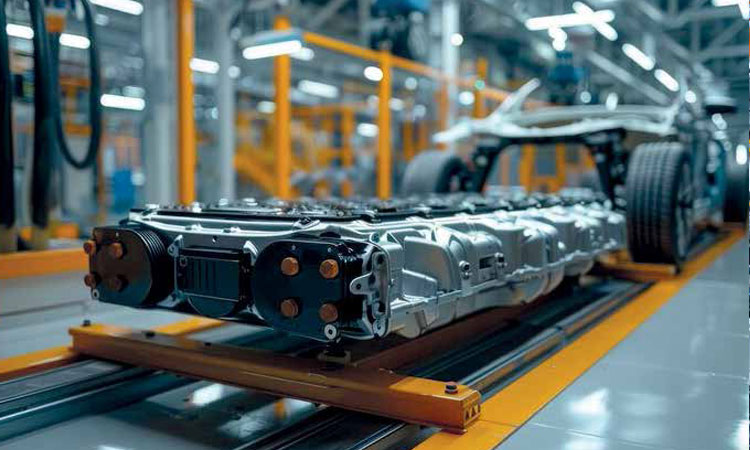
Sustainability and environmental concerns have also influenced the diecasting malaysia, leading companies to adopt eco-friendly practices. With the global push for sustainable manufacturing, die casting companies are exploring ways to reduce their environmental footprint. The use of recyclable materials such as aluminum and zinc alloys has gained popularity, as these metals can be reprocessed without compromising quality. Energy-efficient production methods, waste reduction initiatives, and cleaner manufacturing processes are becoming standard practices within the industry. Malaysian manufacturers are also investing in sustainable technologies, such as electric melting furnaces and closed-loop cooling systems, to minimize energy consumption. These initiatives not only contribute to environmental conservation but also improve cost efficiency and competitiveness in the market. As the demand for sustainable products increases, Malaysia’s die casting industry is well-positioned to meet global expectations for greener manufacturing solutions.
The future of die casting in Malaysia looks promising, with continuous advancements in technology and increasing demand from various industries. The government’s focus on industrial development, along with foreign investments, has created a favorable environment for growth in the manufacturing sector. The adoption of smart manufacturing practices, including robotics, data analytics, and artificial intelligence, is expected to enhance production capabilities and efficiency. As global markets shift towards lightweight and high-performance materials, Malaysia’s die casting industry is set to play a significant role in supplying critical components. By maintaining high-quality standards, investing in research and development, and embracing sustainability, Malaysian manufacturers can strengthen their position in the global die casting industry. With continued innovation and strategic partnerships, Malaysia is poised to remain a competitive force in the die casting sector for years to come.